Аргументация
Причина первая – теплопроводность. Поскольку теплоносители разделены стенкой трубы (как правило, металлической), теплом горячего теплоносителя вначале нагревается эта стенка, а затем уже, от неё – второй, более холодный теплоноситель. Ключевым моментом здесь является теплопроводность материала стенки трубы, то есть – способность быстро и с минимальными потерями забирать тепловую энергию и тут же её отдавать. У металлов, из которых изготавливаются трубы теплообменников (нержавеющей стали, меди и т.д.) теплопроводность находится на весьма высоком уровне.
Иное дело – загрязнения и отложения, образующиеся в теплообменнике в процессе его функционирования. Наиболее часто встречающимся видом является так называемая накипь – минеральные отложения, продукт осаждения на металлических стенках труб различных солей, растворённых в теплоносителе. Накипью эти отложения называют по аналогии с налётом, образующимся в чайнике в процессе его закипания; есть и дополнительное сходство: процесс образования минеральных отложений активизируется при увеличении температуры раствора – у обычной «водопроводной» воды активное образование накипи начинается после превышения границы в 80 градусов Цельсия и далее до точки кипения. Впрочем, и при более низких температурах процесс идёт, только медленнее – всё зависит от характера теплоносителя.
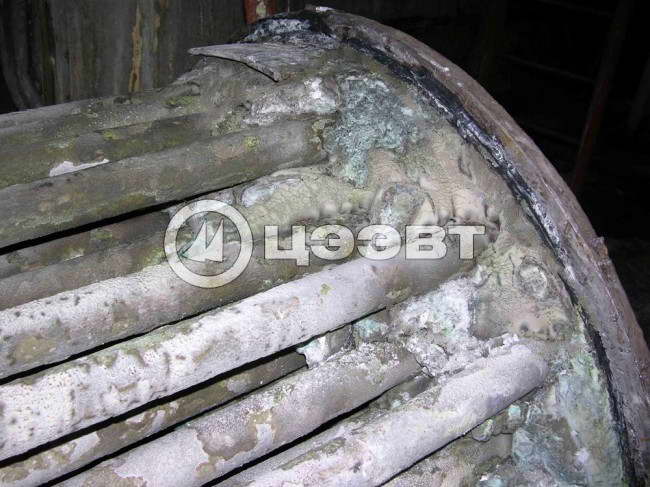
Причина вторая – пропускная способность. Отложения на стенках труб медленно, но верно уменьшают их диаметр. Соответственно, уменьшается и то количество теплоносителя, который за единицу времени может сквозь них пройти; пропорционально снижению потока теплоносителя уменьшается количество тепловой энергии, проходящей через теплообменник, эффективность теплового обмена падает.
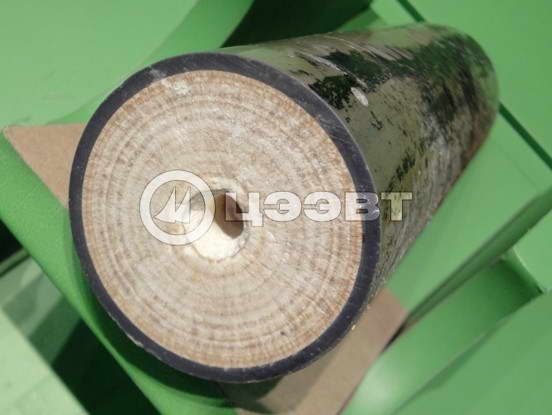
Причина третья – скорость прохождения. При расчёте теплообменника в конструкцию закладываются параметры, обеспечивающие оптимальную скорость движения рабочих сред – такую, чтобы оба теплоносителя в процессе прохождения сквозь агрегат контактировали определённое количество времени, и за это время успевали отдать/получить расчётное количество тепла. Загрязнения меняют эти параметры; баланс нарушается, эффективность обмена снижается.
Скорость прохождения и пропускная способность связаны между собой, так как обе этих величины зависят от реального сечения труб.
Методы борьбы
Методы борьбы с образованием загрязнений и минеральных отложений в теплообменниках можно условно разделить на пассивные и активные. Пассивные методы предполагают превентивное снижение общего уровня загрязнения:
- путём установки в систему подачи теплоносителей различных видов грязевых фильтров («грязевиков») – задерживающих нерастворимые частицы; однако, установка грязевика бессильна против растворённых солей, молекулы которых имеют диаметр значительно меньший, нежели размер фильтрующих ячеек;
- при помощи контроля минерального состава рабочих сред – введением в теплоноситель определённого набора химических веществ, вызывающих выпадение растворённых солей в виде осадка, который может задерживаться фильтром; однако, при высоких объёмах подачи теплоносителей расход реагентов может быть значительным, неоправданным с экономической точки зрения. К тому же, установка электронных анализаторов состава рабочей среды и автоматической системы подачи с насосами высокого противодавления также требуют вложения значительных средств.
Пассивные методы способны существенно замедлить процесс засорения теплообменника, но не прекратить его полностью. Поэтому востребованными остаются методы активного характера – химическая и механическая очистка агрегатов от уже образовавшихся загрязнений. Приехали в столицу, и решили остаться жить в Москве, тогда вам нужен Московский диплом, а для этого нужно – купить диплом в Москве , с дипломом столичного учебного заведения, у вас гораздо больше шансов, найти хорошую работу!.
Химическая очистка
Химическая очистка теплообменников привлекательна с технологической точки зрения прежде всего тем, что не требует разборки агрегата. Это особенно актуально для некоторых видов – в частности, кожухотрубных теплообменников. Такой вид очистки подразумевает подачу в теплообменный аппарат под высоким давлением химически активных веществ, способных растворять накипь и прочие загрязнения. Для ускорения течения реакции раствор предварительно подогревается.
Для проведения химической очистки (промывки) теплообменных аппаратов требуется наличие не только соответствующих химикатов, но и специального оборудования. В упрощённом виде установку для промывки теплообменников можно представить в виде ёмкости с химическим реагентом, насоса высокого давления и нагревательного элемента. Вероятно также наличие фильтра для очистки реагента, уже прошедшего теплообменник, от нерастворённых остатков загрязнений – с целью его повторного использования.
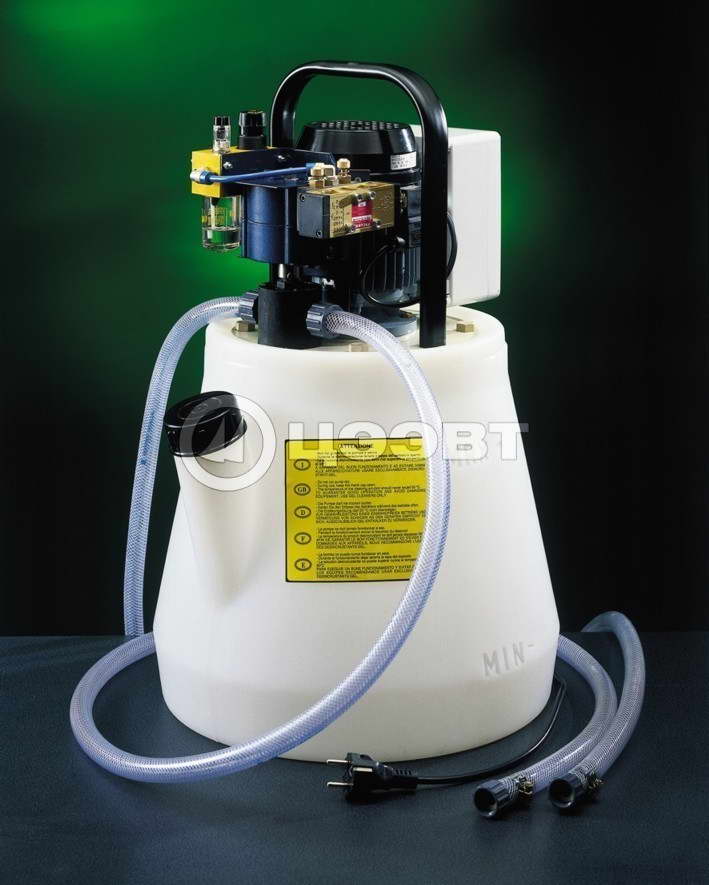
Несмотря на относительную простоту процесса химической очистки теплообменника, у него есть и свои недостатки.
- Во-первых, при сильных загрязнениях процесс может занять достаточно длительное время.
- Во-вторых, некоторые части теплообменника – незагрязнённые или уже очищенные – всё это время будут контактировать с химически активными веществами, используемыми для промывки; а это может вызвать ощутимую коррозию металла.
- В-третьих, без разборки теплообменника сложно визуально проконтролировать качество промывки – некоторые участки внутренней поверхности могут остаться не очищенными.
Механическая очистка
Механическая очистка теплообменников, в отличие от химической, в любом случае подразумевает частичную или полную разборку агрегата. В случае с кожухотрубными теплообменниками это означает как минимум демонтаж распределительных камер для доступа к трубной решётке и внутренней поверхности труб трубного пучка.
После очистки поверхности камер и трубной решётки при помощи пескоструйного аппарата или иным доступным методом, наступает очередь труб – в них вводится жёсткий или гибкий стержень с длиной не менее половины длины трубы и с рабочим инструментом на конце – сверлом, фрезой, радиальной металлической щёткой и т.д. Стержень, как правило, полый; к его торцу прикладывается вращательное усилие от ручного, чаще – электромеханического привода. Вращаясь, стержень с инструментом на конце снимает отложения с поверхности труб. Одновременно сквозь канал в стержне подаётся промывочная жидкость, которая смазывает область приложения инструмента и вымывает частицы снятого слоя загрязнений.
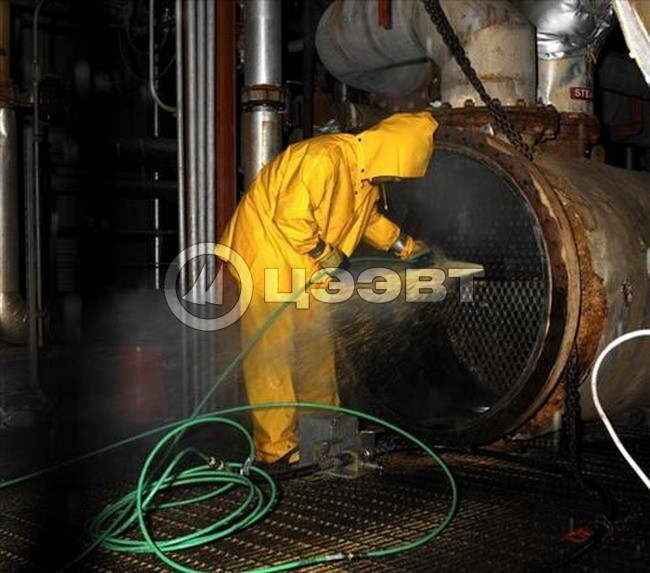
АО «ЦЭЭВТ» производит теплообменные аппараты в сборе для установки в новые системы или взамен выработавших свой ресурс агрегатов, а также отдельно изготавливает трубные пучки с улучшенными характеристиками труб – для установки в аппараты отечественного и зарубежного производства. Каждый теплообменник или трубный пучок, предназначенный для замены, изготавливается по индивидуальному проекту с учётом конкретных технических условий и требований эксплуатации.
При этом, в расчёт проекта вводится дополнительный параметр – термическое сопротивление загрязняющих отложений. По сути, закладывается некоторый запас, позволяющий эксплуатировать теплообменный аппарат в расчётном режиме даже после образования на поверхностях теплообмена определённого слоя загрязнений.